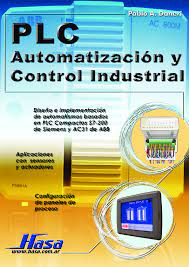
Automatización Industrial con PLC: Optimización de Procesos y Documentación en Formato PDF
La automatización industrial y el PLC (Controlador Lógico Programable) han revolucionado la forma en que se llevan a cabo los procesos de producción en diversas industrias. En este artículo, exploraremos la importancia de la automatización industrial y cómo el uso de PLC ha mejorado la eficiencia y la productividad en el sector manufacturero.
La automatización industrial se refiere al uso de tecnología para controlar y operar maquinaria y procesos en una planta de producción. Anteriormente, estos procesos dependían en gran medida del trabajo manual, lo que llevaba a una mayor posibilidad de errores humanos, baja eficiencia y costos operativos elevados. Sin embargo, con la introducción de la automatización industrial, las empresas han logrado optimizar sus operaciones.
Un componente clave de la automatización industrial es el PLC. El PLC es un dispositivo electrónico programable que utiliza lógica digital para controlar máquinas y procesos industriales. Estos dispositivos son altamente confiables y se utilizan ampliamente debido a su capacidad para realizar múltiples tareas simultáneamente, monitorear variables clave y responder rápidamente a cambios en los procesos.
Una ventaja significativa del uso de PLC es su capacidad para almacenar programas complejos que permiten controlar una amplia gama de equipos industriales. Esto significa que los operadores pueden programar fácilmente el PLC para realizar diversas tareas, como controlar motores, regular temperaturas, gestionar sistemas de seguridad e incluso recopilar datos para análisis posteriores.
Además, el uso de PLC ha permitido reducir significativamente los tiempos de inactividad en las plantas industriales. Los PLC son capaces de diagnosticar rápidamente problemas técnicos y, en muchos casos, solucionarlos automáticamente. Esto no solo ahorra tiempo valioso, sino que también disminuye los costos asociados con la reparación y el mantenimiento.
Otra ventaja importante de la automatización industrial y el PLC es su capacidad para mejorar la seguridad en el lugar de trabajo. Los PLC pueden integrar sistemas de seguridad avanzados que monitorean constantemente las condiciones peligrosas y toman medidas preventivas para evitar accidentes. Esto garantiza un entorno laboral más seguro para los empleados y reduce los riesgos asociados con la operación de maquinaria pesada.
En resumen, la automatización industrial y el uso de PLC han transformado por completo la forma en que se llevan a cabo los procesos de producción en diversas industrias. Estas tecnologías han mejorado la eficiencia, reducido los tiempos de inactividad, aumentado la seguridad laboral y disminuido los costos operativos. A medida que avanza la tecnología, es probable que veamos aún más avances en este campo, lo que llevará a una mayor optimización y mejora continua en las operaciones industriales.
5 Preguntas Frecuentes sobre Automatización Industrial PLC en formato PDF
- ¿Dónde puedo descargar un manual de automatización industrial PLC en formato PDF?
- ¿Qué es un programa PLC y cómo funciona?
- ¿Cómo se programan los PLC para controlar procesos industriales?
- ¿Cuáles son las principales ventajas de la automatización industrial con PLCs?
- ¿Cuáles son los principales componentes de un sistema de automatización industrial con PLCs?
¿Dónde puedo descargar un manual de automatización industrial PLC en formato PDF?
Existen varias opciones para descargar manuales de automatización industrial PLC en formato PDF. Aquí te mencionaré algunas fuentes confiables donde podrías encontrar dichos manuales:
- Sitios web de fabricantes: Muchos fabricantes de PLC ofrecen manuales y documentación técnica en sus sitios web oficiales. Algunos ejemplos conocidos son Siemens, Allen-Bradley (Rockwell Automation), Schneider Electric, Mitsubishi Electric, entre otros. Visita los sitios web de estos fabricantes y busca la sección de descargas o soporte técnico para encontrar los manuales en formato PDF.
- Plataformas educativas y académicas: Algunas plataformas educativas y académicas ofrecen recursos gratuitos relacionados con la automatización industrial y PLC. Puedes buscar en sitios como SlideShare, Scribd o Academia.edu, donde podrías encontrar presentaciones o documentos técnicos sobre el tema.
- Foros y comunidades en línea: Participar en foros y comunidades en línea dedicadas a la automatización industrial puede ser una excelente manera de obtener información valiosa y acceder a manuales compartidos por otros profesionales del campo. Algunos foros populares son PLCs.net, Eng-Tips o AutomationDirect Forum.
Recuerda siempre verificar la fuente y asegurarte de que los manuales descargados provengan de fuentes confiables y estén actualizados según el modelo específico del PLC que estés utilizando. Además, ten en cuenta que algunos fabricantes pueden requerir un registro previo o una cuenta para acceder a ciertos recursos técnicos.
¿Qué es un programa PLC y cómo funciona?
Un programa PLC, también conocido como programa de Controlador Lógico Programable, es un conjunto de instrucciones escritas en un lenguaje específico que se utiliza para controlar y operar un PLC (Controlador Lógico Programable).
El programa PLC se crea utilizando un software especializado que permite al usuario definir las diferentes tareas y funciones que el PLC debe realizar. Estas tareas pueden incluir desde el control de motores y válvulas hasta la regulación de temperaturas, el monitoreo de sensores y la comunicación con otros dispositivos.
El programa PLC se estructura en una serie de bloques o secciones que contienen las instrucciones necesarias para llevar a cabo una determinada función. Estas instrucciones pueden ser lógicas (AND, OR, NOT), aritméticas (suma, resta), de temporización (retardos) o incluso instrucciones especiales diseñadas para tareas específicas.
Una vez que el programa PLC ha sido creado, se carga en la memoria del controlador mediante una conexión física o inalámbrica. El PLC ejecuta las instrucciones secuencialmente y en tiempo real, es decir, a medida que los eventos ocurren en la planta o proceso industrial.
El funcionamiento del programa PLC se basa en ciclos repetitivos llamados «escaneos». Durante cada escaneo, el controlador verifica las entradas (sensores) para detectar cambios o eventos. Luego procesa las instrucciones del programa según lo definido por el usuario. Por último, actualiza las salidas (actuadores) según los resultados obtenidos.
Es importante destacar que los programas PLC son altamente flexibles y pueden ser modificados o actualizados según sea necesario sin necesidad de reemplazar el hardware del controlador. Esto permite adaptar el sistema a cambios en los procesos de producción o implementar mejoras sin interrumpir la operación.
En resumen, un programa PLC es un conjunto de instrucciones que se utilizan para controlar y operar un Controlador Lógico Programable. Estas instrucciones se crean utilizando software especializado y definen las tareas y funciones que el PLC debe realizar. El programa es cargado en la memoria del controlador y se ejecuta secuencialmente en ciclos repetitivos, permitiendo el control en tiempo real de los procesos industriales.
¿Cómo se programan los PLC para controlar procesos industriales?
La programación de un PLC para controlar procesos industriales implica seguir una serie de pasos. Aquí te presento una descripción general del proceso:
- Análisis y diseño: En esta etapa, es importante comprender los requisitos y objetivos del proceso industrial que se va a controlar. Se debe identificar qué entradas y salidas son necesarias, qué acciones se deben realizar y cómo se deben manejar las situaciones excepcionales.
- Selección del software: Existen diferentes software de programación de PLC en el mercado. Es importante seleccionar el que mejor se adapte a las necesidades específicas del proceso y tener en cuenta la compatibilidad con el modelo de PLC utilizado.
- Configuración del hardware: Antes de comenzar con la programación, es necesario configurar físicamente el hardware del PLC. Esto incluye conectar los módulos de E/S (Entrada/Salida), sensores, actuadores y cualquier otro dispositivo necesario.
- Desarrollo del programa: Utilizando el software seleccionado, se procede a desarrollar el programa para el PLC. La programación se realiza utilizando lenguajes específicos para PLC, como Ladder Diagram (LD), Function Block Diagram (FBD) o Structured Text (ST). Estos lenguajes permiten definir las condiciones lógicas, las acciones a realizar y los tiempos de ejecución.
- Pruebas y depuración: Una vez finalizado el programa, es fundamental realizar pruebas exhaustivas para verificar su correcto funcionamiento. Durante esta etapa, se pueden simular diferentes situaciones para asegurarse de que el programa responda adecuadamente a todas las condiciones esperadas.
- Implementación: Una vez que se ha probado y depurado el programa, se carga en el PLC. Esto implica transferir el programa desde el software de programación al PLC utilizando una conexión física, como un cable de comunicación.
- Monitoreo y ajustes: Después de la implementación, es importante monitorear el funcionamiento del PLC y realizar ajustes si es necesario. Esto puede implicar cambios en las condiciones lógicas, tiempos de ejecución o acciones a realizar.
Es importante destacar que la programación de PLC requiere conocimientos técnicos y experiencia en automatización industrial. Si no tienes experiencia previa en este campo, es recomendable buscar la asistencia de profesionales capacitados para garantizar un control eficiente y seguro de los procesos industriales.
¿Cuáles son las principales ventajas de la automatización industrial con PLCs?
La automatización industrial con PLCs (Controladores Lógicos Programables) ofrece una serie de ventajas significativas para las empresas en diversos sectores. A continuación, se presentan algunas de las principales ventajas de la automatización industrial con PLCs:
- Mejora de la eficiencia: La automatización industrial permite realizar tareas repetitivas y monótonas de manera más rápida y precisa que los trabajadores humanos. Los PLCs pueden realizar múltiples tareas simultáneamente, lo que aumenta la productividad y reduce los tiempos de producción.
- Reducción de errores: Los PLCs están diseñados para seguir instrucciones precisas y no cometer errores humanos. Esto garantiza una mayor precisión en los procesos industriales, minimizando así los errores y desperdicios que pueden ocurrir debido a la intervención humana.
- Flexibilidad en la programación: Los PLCs permiten una programación flexible, lo que significa que se pueden modificar rápidamente para adaptarse a diferentes requisitos o cambios en el proceso de producción. Esto proporciona a las empresas la capacidad de ajustar y optimizar sus operaciones según sea necesario.
- Mayor seguridad: Los PLCs ofrecen funciones avanzadas de seguridad, como sistemas de parada de emergencia y monitoreo constante de condiciones peligrosas. Esto ayuda a prevenir accidentes laborales y garantiza un entorno seguro para los trabajadores.
- Diagnóstico rápido y mantenimiento predictivo: Los PLCs tienen la capacidad de monitorear constantemente el estado del equipo y detectar posibles problemas antes de que se conviertan en fallas importantes. Esto permite un mantenimiento predictivo, evitando tiempos muertos innecesarios y reduciendo los costos de reparación.
- Recopilación y análisis de datos: Los PLCs pueden recopilar datos en tiempo real sobre el rendimiento del equipo y los procesos industriales. Estos datos se pueden utilizar para realizar análisis y tomar decisiones informadas para mejorar la eficiencia y optimizar la producción.
- Reducción de costos: La automatización industrial con PLCs puede ayudar a reducir los costos operativos al disminuir la necesidad de mano de obra, minimizar los errores y desperdicios, optimizar el uso de recursos y mejorar la eficiencia energética.
En general, la automatización industrial con PLCs ofrece una serie de ventajas clave que permiten a las empresas mejorar su productividad, calidad, seguridad y rentabilidad. Estas ventajas hacen que la implementación de PLCs sea una opción atractiva para muchas industrias en busca de optimizar sus procesos de producción.
¿Cuáles son los principales componentes de un sistema de automatización industrial con PLCs?
Un sistema de automatización industrial con PLCs (Controladores Lógicos Programables) consta de varios componentes clave que trabajan en conjunto para controlar y monitorear los procesos industriales. A continuación, se presentan los principales componentes de un sistema de automatización industrial con PLCs:
- Controlador PLC: Es el cerebro del sistema y se encarga de ejecutar el programa que controla las operaciones del proceso. El controlador PLC puede ser programado para realizar diferentes tareas, como recibir señales de entrada, procesar la información y generar señales de salida para controlar dispositivos y maquinaria.
- Módulos de E/S (Entrada/Salida): Son dispositivos que permiten la comunicación entre el controlador PLC y los sensores, actuadores y otros equipos del proceso industrial. Los módulos de entrada reciben señales físicas del entorno, como temperatura, presión o nivel, mientras que los módulos de salida envían señales a los actuadores para controlar motores, válvulas o luces.
- Sensores: Son dispositivos utilizados para medir variables físicas o químicas en el proceso industrial. Pueden incluir sensores de temperatura, presión, flujo, nivel u otros tipos específicos según las necesidades del proceso.
- Actuadores: Son dispositivos utilizados para realizar acciones físicas en respuesta a las señales generadas por el controlador PLC. Los actuadores pueden ser motores eléctricos, cilindros neumáticos o válvulas hidráulicas que realizan movimientos mecánicos necesarios en el proceso.
- Interfaz Hombre-Máquina (HMI): Es una interfaz gráfica que permite a los operadores interactuar con el sistema de automatización. A través de una pantalla táctil, los operadores pueden monitorear el estado del proceso, realizar ajustes y recibir información en tiempo real.
- Redes de Comunicación: Son utilizadas para conectar todos los componentes del sistema, permitiendo la transferencia de datos entre ellos. Las redes pueden ser Ethernet, Profibus, Modbus u otras tecnologías según las necesidades del sistema.
- Software de Programación: Se utiliza para desarrollar y cargar programas en el controlador PLC. Los programadores utilizan software específico para crear la lógica y las secuencias de control que definirán el comportamiento del sistema.
Estos son solo algunos de los principales componentes de un sistema de automatización industrial con PLCs. Cada sistema puede variar en función de las necesidades específicas del proceso industrial al que se aplica. La combinación adecuada de estos componentes permite controlar y optimizar eficientemente los procesos industriales para mejorar la productividad y la eficiencia en diversas aplicaciones industriales.
Leave a Reply