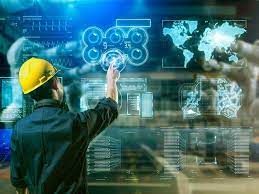
Optimización y Eficiencia: La Automatización de los Procesos de Manufactura
La automatización de los procesos de manufactura es una tendencia creciente en la industria actual. Con avances tecnológicos como la inteligencia artificial, el Internet de las cosas y la robótica, las empresas están adoptando cada vez más esta forma de mejorar su eficiencia, productividad y rentabilidad.
La automatización de los procesos de manufactura implica el uso de máquinas y sistemas controlados por computadora para realizar tareas que anteriormente eran realizadas por trabajadores humanos. Esto no significa que los seres humanos sean reemplazados por completo, sino que se les libera de tareas repetitivas y tediosas para enfocarse en actividades más creativas y estratégicas.
Uno de los principales beneficios de la automatización es la mejora en la precisión y calidad del trabajo realizado. Las máquinas pueden ejecutar tareas con una precisión milimétrica, minimizando errores humanos y reduciendo el desperdicio. Esto se traduce en productos finales de mayor calidad y satisface las expectativas cada vez más altas de los consumidores.
Además, la automatización permite una mayor velocidad en la producción. Las máquinas pueden trabajar a velocidades constantes sin fatiga ni necesidad de descanso, lo que acelera el tiempo necesario para fabricar un producto. Esto es especialmente beneficioso para las empresas que tienen altas demandas o plazos ajustados.
Otro aspecto clave es el aumento en la eficiencia operativa. La automatización reduce los tiempos improductivos al eliminar demoras asociadas con cambios entre tareas o con descansos del personal. Además, los sistemas automatizados pueden funcionar las 24 horas del día sin interrupciones, lo que optimiza la capacidad de producción y reduce los costos asociados con el tiempo de inactividad.
La seguridad también es un aspecto importante a considerar. Al automatizar tareas peligrosas o que implican riesgos para los trabajadores, se reducen los accidentes laborales y se garantiza un entorno de trabajo más seguro. Las máquinas pueden realizar actividades en entornos hostiles o con sustancias peligrosas sin poner en riesgo la salud de los empleados.
Sin embargo, es importante tener en cuenta que la implementación de la automatización no está exenta de desafíos. Requiere una inversión inicial significativa en tecnología y capacitación del personal. Además, puede generar preocupaciones sobre la pérdida de puestos de trabajo para los trabajadores no calificados.
En conclusión, la automatización de los procesos de manufactura es una tendencia que está transformando la industria. A través de la incorporación de tecnologías avanzadas, las empresas pueden mejorar su eficiencia, calidad y seguridad en un mundo cada vez más competitivo. Si bien presenta desafíos, el potencial para el crecimiento y el éxito a largo plazo hace que valga la pena considerar su implementación.
7 Preguntas Frecuentes sobre la Automatización de los Procesos de Manufactura
- ¿Qué es la automatización de los procesos de manufactura?
- ¿Cuáles son los beneficios de la automatización de los procesos de manufactura?
- ¿Cuáles son las principales tecnologías utilizadas para la automatización de los procesos de manufactura?
- ¿Cómo se implementa un sistema de automatización en una planta industrial?
- ¿Qué tipo de riesgos implica el uso de la automatización en los procesos industriales?
- ¿Qué factores hay que considerar al elegir un sistema para la automatización industrial?
- ¿Cómo se puede mejorar y optimizar el rendimiento del sistema con el tiempo?
¿Qué es la automatización de los procesos de manufactura?
La automatización de los procesos de manufactura se refiere a la implementación de sistemas y tecnologías para realizar tareas en el ámbito de la producción industrial de manera automatizada, es decir, sin la intervención directa de los trabajadores. Consiste en utilizar máquinas, robots y sistemas controlados por computadora para llevar a cabo actividades que antes eran realizadas manualmente.
Estos procesos automatizados pueden abarcar desde tareas simples y repetitivas hasta operaciones más complejas que requieren un alto grado de precisión. Algunas de las actividades que se pueden automatizar incluyen ensamblaje, manipulación de materiales, control de calidad, embalaje y etiquetado, entre otras.
La automatización puede implicar el uso de sensores y dispositivos para monitorear y controlar el flujo del proceso productivo. Estos dispositivos recopilan datos en tiempo real sobre parámetros como temperatura, presión, velocidad o posición, permitiendo ajustes automáticos para mantener la calidad y eficiencia del proceso.
Además, la automatización puede involucrar el uso de software especializado que permite programar las máquinas y robots para realizar determinadas tareas. Esto implica definir secuencias lógicas y establecer criterios específicos para que los equipos actúen según las necesidades del proceso.
La implementación de la automatización en los procesos de manufactura tiene como objetivo principal mejorar la eficiencia operativa al reducir tiempos improductivos y minimizar errores humanos. También busca aumentar la productividad al acelerar el ritmo de producción y optimizar los recursos utilizados.
Al mismo tiempo, la automatización puede mejorar la calidad del producto final al reducir defectos o variaciones no deseadas. Además, puede contribuir a la seguridad laboral al eliminar o reducir la exposición de los trabajadores a tareas peligrosas o repetitivas.
En resumen, la automatización de los procesos de manufactura implica el uso de tecnologías y sistemas para realizar tareas productivas sin intervención humana directa. Su implementación busca mejorar la eficiencia, calidad y seguridad en el ámbito industrial, permitiendo una producción más rápida, precisa y rentable.
¿Cuáles son los beneficios de la automatización de los procesos de manufactura?
La automatización de los procesos de manufactura ofrece una serie de beneficios significativos para las empresas. Aquí hay algunos de ellos:
- Mejora en la eficiencia: La automatización permite realizar tareas repetitivas y tediosas de manera más rápida y precisa que los seres humanos. Esto reduce los tiempos improductivos, como cambios entre tareas o descansos del personal, lo que resulta en una mayor eficiencia operativa y una producción más rápida.
- Aumento en la productividad: Las máquinas automatizadas pueden trabajar a velocidades constantes sin fatiga ni necesidad de descanso. Esto acelera el tiempo necesario para fabricar un producto y aumenta la capacidad de producción, lo que permite cumplir con mayores demandas y plazos ajustados.
- Mejora en la calidad del producto: La precisión milimétrica de las máquinas automatizadas reduce los errores humanos y minimiza el desperdicio. Esto se traduce en productos finales de mayor calidad, lo que satisface las expectativas cada vez más altas de los consumidores.
- Mayor seguridad laboral: La automatización permite reemplazar tareas peligrosas o riesgosas para los trabajadores por máquinas controladas por computadora. Esto reduce el riesgo de accidentes laborales y crea un entorno de trabajo más seguro.
- Reducción de costos: Aunque la implementación inicial puede requerir una inversión significativa, a largo plazo, la automatización puede ayudar a reducir costos operativos. Al minimizar errores y desperdicio, así como al optimizar la capacidad de producción, se pueden obtener ahorros significativos.
- Flexibilidad y adaptabilidad: Los sistemas automatizados pueden ser reprogramados y reconfigurados rápidamente para adaptarse a cambios en la demanda o en los requisitos del producto. Esto proporciona una mayor flexibilidad para responder a las necesidades del mercado y mantenerse competitivo.
- Mejor aprovechamiento de los recursos: La automatización permite utilizar de manera más eficiente los recursos disponibles, como materiales, energía y mano de obra. Esto contribuye a una gestión más sostenible y responsable desde el punto de vista medioambiental.
En resumen, la automatización de los procesos de manufactura ofrece beneficios como mayor eficiencia, productividad y calidad del producto, así como una mejora en la seguridad laboral y una reducción de costos operativos. Estos beneficios ayudan a las empresas a mantenerse competitivas en un entorno empresarial cada vez más exigente.
¿Cuáles son las principales tecnologías utilizadas para la automatización de los procesos de manufactura?
La automatización de los procesos de manufactura se basa en una variedad de tecnologías avanzadas que permiten la ejecución eficiente y precisa de tareas. A continuación, se presentan algunas de las principales tecnologías utilizadas en este campo:
- Robótica: Los robots industriales desempeñan un papel fundamental en la automatización de la manufactura. Estos robots son programados para realizar tareas específicas, como ensamblaje, soldadura, manipulación de materiales y empaquetado. Utilizan sensores y sistemas de visión artificial para interactuar con su entorno y llevar a cabo las tareas asignadas.
- Control numérico computarizado (CNC): Esta tecnología permite controlar máquinas herramientas mediante instrucciones codificadas en software. Los sistemas CNC son ampliamente utilizados en procesos como el fresado, torneado, corte por láser y mecanizado en general. Proporcionan una alta precisión y repetibilidad en la fabricación de piezas.
- Internet de las cosas (IoT): La interconexión de dispositivos a través del IoT permite recopilar datos en tiempo real sobre el estado y rendimiento de los equipos utilizados en los procesos de manufactura. Esto facilita el monitoreo remoto, el análisis predictivo y la optimización del rendimiento, lo que contribuye a una mayor eficiencia operativa.
- Inteligencia Artificial (IA): La IA desempeña un papel crucial al permitir que los sistemas automatizados aprendan, adapten y tomen decisiones basadas en datos. Algoritmos avanzados pueden analizar grandes cantidades de información para mejorar la calidad del producto, predecir fallas en la maquinaria y optimizar los procesos de producción.
- Visión artificial: Los sistemas de visión artificial utilizan cámaras y algoritmos para inspeccionar y analizar imágenes o videos en tiempo real. Esto permite la detección de defectos, el reconocimiento de patrones, la lectura de códigos de barras y otras aplicaciones que requieren una percepción visual precisa.
- Automatización del flujo de trabajo: Mediante el uso de software especializado, se pueden automatizar tareas administrativas y de gestión, como la programación de producción, el seguimiento del inventario y la planificación logística. Esto agiliza los procesos internos y mejora la coordinación entre diferentes áreas.
Estas son solo algunas de las tecnologías más utilizadas en la automatización de los procesos de manufactura. A medida que avanza la innovación tecnológica, es probable que surjan nuevas herramientas y enfoques que seguirán impulsando la eficiencia y productividad en este campo.
¿Cómo se implementa un sistema de automatización en una planta industrial?
La implementación de un sistema de automatización en una planta industrial requiere una planificación cuidadosa y un enfoque paso a paso. Aquí hay algunos pasos clave a considerar:
- Evaluación de necesidades: Comienza por evaluar las necesidades específicas de tu planta industrial. Identifica los procesos que podrían beneficiarse de la automatización y establece los objetivos que deseas lograr con la implementación.
- Investigación y selección de tecnología: Investiga las diferentes tecnologías disponibles en el mercado que se ajusten a tus necesidades. Considera aspectos como la capacidad, la compatibilidad con tus sistemas existentes, el costo y el soporte técnico.
- Diseño del sistema: Una vez que hayas seleccionado la tecnología adecuada, trabaja en el diseño del sistema de automatización. Define cómo se integrará con los procesos existentes, qué tareas se automatizarán y cómo se comunicarán los diferentes componentes del sistema.
- Adquisición e instalación: Adquiere los equipos y componentes necesarios para el sistema de automatización. Asegúrate de contar con personal capacitado para realizar la instalación adecuada y garantizar su correcto funcionamiento.
- Programación y configuración: Configura los parámetros del sistema de acuerdo con tus requisitos específicos. Programa las secuencias de trabajo, las instrucciones para cada tarea automatizada y asegúrate de que todas las funciones estén correctamente configuradas.
- Pruebas y ajustes: Realiza pruebas exhaustivas del sistema para verificar su funcionamiento correcto. Realiza ajustes si es necesario para optimizar su rendimiento.
- Capacitación del personal: Proporciona capacitación adecuada a tu personal sobre cómo operar y mantener el sistema de automatización. Asegúrate de que comprendan cómo interactuar con él y solucionar problemas básicos.
- Implementación gradual: Puedes optar por implementar el sistema de automatización en etapas, comenzando por procesos menos críticos o áreas específicas. Esto permitirá una transición más fluida y la capacidad de realizar ajustes según sea necesario.
- Monitoreo y mantenimiento: Establece un programa de monitoreo regular para asegurarte de que el sistema funcione correctamente y detectar posibles problemas a tiempo. Realiza mantenimiento preventivo para garantizar su rendimiento a largo plazo.
- Mejora continua: La implementación del sistema de automatización es solo el comienzo. Busca constantemente formas de mejorar y optimizar el sistema a medida que adquieras más experiencia y obtengas retroalimentación del personal y los resultados obtenidos.
Recuerda que cada planta industrial es única, por lo que es importante adaptar estos pasos a tus necesidades específicas. Además, contar con la asesoría de expertos en automatización puede ser beneficioso para garantizar una implementación exitosa.
¿Qué tipo de riesgos implica el uso de la automatización en los procesos industriales?
Si bien la automatización de los procesos industriales ofrece numerosos beneficios, también implica ciertos riesgos que deben ser considerados. Algunos de los riesgos asociados con el uso de la automatización son:
- Pérdida de empleo: La automatización puede resultar en la reducción de puestos de trabajo, especialmente aquellos que implican tareas repetitivas y rutinarias. Los trabajadores pueden enfrentar dificultades para adaptarse a los nuevos roles o necesitar capacitación adicional para trabajar con las tecnologías automatizadas.
- Dependencia tecnológica: Las empresas que dependen en gran medida de la automatización pueden enfrentar desafíos si se producen fallas técnicas o interrupciones en los sistemas automatizados. Esto puede llevar a una disminución temporal o incluso a una paralización completa de la producción hasta que se resuelvan los problemas técnicos.
- Costos iniciales y mantenimiento: La implementación y el mantenimiento de sistemas automatizados pueden requerir una inversión inicial significativa. Además, es necesario contar con personal capacitado para operar y mantener estos sistemas, lo que puede generar costos adicionales.
- Vulnerabilidad a ciberataques: Con el aumento del uso de tecnologías conectadas a Internet, existe un mayor riesgo de ciberataques dirigidos a sistemas automatizados. Los hackers pueden intentar acceder a los sistemas industriales para robar información confidencial o interrumpir las operaciones.
- Falta de flexibilidad: Los sistemas automatizados están diseñados para realizar tareas específicas según un conjunto predefinido de instrucciones. Esto puede limitar la capacidad de adaptarse rápidamente a cambios en la demanda del mercado o en las necesidades de producción, lo que puede afectar la capacidad de respuesta de la empresa.
- Impacto social: La automatización puede tener un impacto negativo en las comunidades y regiones donde se encuentran las industrias afectadas. La pérdida de empleos puede provocar desigualdades económicas y sociales, así como tensiones en el mercado laboral.
Es importante destacar que estos riesgos no deben disuadir a las empresas de adoptar la automatización, sino que deben ser considerados y gestionados adecuadamente. La planificación cuidadosa, la capacitación del personal y la implementación gradual pueden ayudar a minimizar los riesgos asociados con el uso de la automatización en los procesos industriales.
¿Qué factores hay que considerar al elegir un sistema para la automatización industrial?
Al elegir un sistema para la automatización industrial, es importante considerar varios factores clave. Estos factores ayudarán a garantizar que el sistema seleccionado se ajuste a las necesidades y objetivos específicos de la empresa. A continuación, se presentan algunos aspectos importantes a tener en cuenta:
- Objetivos y requisitos: Antes de elegir un sistema de automatización industrial, es fundamental comprender claramente los objetivos comerciales y los requisitos específicos que se desean lograr. Esto incluye identificar qué procesos se deben automatizar, qué mejoras se esperan en términos de eficiencia, productividad o calidad, y cuáles son las necesidades particulares de la empresa.
- Escalabilidad: Es importante considerar si el sistema de automatización es escalable, es decir, si puede adaptarse y crecer junto con las necesidades cambiantes de la empresa. La capacidad de agregar nuevas funciones o ampliar el sistema en el futuro es crucial para garantizar una inversión a largo plazo.
- Compatibilidad: El sistema de automatización debe ser compatible con los equipos y maquinarias existentes en la planta o fábrica. Es necesario evaluar si el sistema puede integrarse sin problemas con los dispositivos y sistemas ya utilizados para evitar problemas de interoperabilidad.
- Flexibilidad: La capacidad del sistema para adaptarse a diferentes tipos de procesos y productos es otro factor importante a considerar. La flexibilidad permite realizar cambios rápidos en la producción o adaptarse a nuevas demandas del mercado sin requerir una reconfiguración completa del sistema.
- Facilidad de uso e interfaz intuitiva: Un buen sistema de automatización debe ser fácil de usar para los operadores y técnicos encargados de su funcionamiento. Una interfaz intuitiva y amigable facilitará la configuración, programación y supervisión del sistema, reduciendo el tiempo de aprendizaje y los posibles errores humanos.
- Soporte técnico y capacitación: Es importante considerar si el proveedor del sistema ofrece un buen soporte técnico y capacitación adecuada para los usuarios finales. Esto garantiza que la empresa pueda resolver cualquier problema o dificultad que pueda surgir durante la implementación o el uso continuo del sistema.
- Costo total de propiedad: Además del costo inicial de adquisición, es esencial evaluar el costo total de propiedad a lo largo del tiempo. Esto incluye los costos asociados con el mantenimiento, actualizaciones, repuestos y posibles mejoras futuras.
- Seguridad: La seguridad es un factor crítico en la automatización industrial. Es necesario asegurarse de que el sistema cumpla con los estándares de seguridad requeridos para proteger tanto a los trabajadores como a las instalaciones.
Al considerar estos factores al elegir un sistema para la automatización industrial, las empresas pueden tomar decisiones informadas que les permitan aprovechar al máximo esta tecnología y obtener beneficios significativos en términos de eficiencia, productividad y competitividad en el mercado.
¿Cómo se puede mejorar y optimizar el rendimiento del sistema con el tiempo?
Mejorar y optimizar el rendimiento del sistema con el tiempo es un objetivo clave para garantizar la eficiencia y el éxito continuo de cualquier empresa. Aquí hay algunas estrategias que se pueden implementar:
- Monitoreo constante: Es fundamental realizar un seguimiento regular del rendimiento del sistema a través de herramientas de monitoreo y análisis. Esto permite identificar posibles cuellos de botella, problemas de rendimiento o áreas que requieren mejoras.
- Actualizaciones y parches: Mantener el sistema actualizado con las últimas versiones de software, parches de seguridad y actualizaciones es esencial para mejorar su rendimiento. Las actualizaciones suelen incluir mejoras en la velocidad, estabilidad y funcionalidad del sistema.
- Optimización del hardware: Evaluar periódicamente el hardware utilizado en el sistema puede ayudar a identificar oportunidades para mejorar su rendimiento. Esto puede implicar agregar más capacidad de almacenamiento, aumentar la memoria RAM o actualizar los procesadores.
- Optimización del software: Revisar regularmente las configuraciones del software utilizado en el sistema puede ayudar a identificar ajustes que mejoren su rendimiento. Esto puede incluir la optimización de bases de datos, ajustes en los algoritmos utilizados o la eliminación de funciones innecesarias.
- Capacitación y desarrollo del personal: Brindar capacitación continua al personal encargado del sistema ayuda a mejorar su conocimiento y habilidades técnicas, lo que a su vez contribuye a una mejor gestión y optimización del rendimiento.
- Análisis de datos: Utilizar herramientas analíticas para recopilar datos sobre el rendimiento del sistema puede proporcionar información valiosa sobre áreas problemáticas o ineficiencias. Esto permite tomar decisiones informadas y realizar mejoras específicas.
- Optimización de la red: Si el sistema depende de una red, es importante optimizarla para garantizar una comunicación eficiente y rápida entre los distintos componentes del sistema. Esto puede incluir la implementación de tecnologías de red más rápidas o la optimización de la configuración de la red existente.
- Automatización: La automatización de tareas repetitivas y rutinarias puede liberar recursos y mejorar el rendimiento general del sistema. Al delegar estas tareas a sistemas automatizados, se reduce el riesgo de errores humanos y se mejora la eficiencia en general.
En resumen, mejorar y optimizar el rendimiento del sistema con el tiempo requiere un enfoque constante en la monitorización, actualizaciones, optimizaciones tanto a nivel de hardware como software, capacitación del personal y análisis continuo de datos. Al implementar estas estrategias, las empresas pueden garantizar un rendimiento óptimo que se adapte a las necesidades cambiantes del entorno empresarial.
Leave a Reply