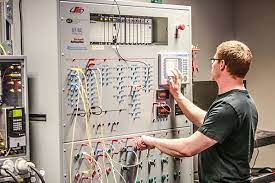
Optimización Industrial: El Control PLC como Pilar de la Automatización
PLC Control: La Automatización Industrial al Servicio de la Eficiencia
En el mundo de la industria, la eficiencia y la productividad son dos factores clave para el éxito de cualquier empresa. Es por eso que cada vez más compañías están recurriendo a la automatización industrial como una forma de optimizar sus procesos y mejorar su rendimiento. En este sentido, el control PLC (Programmable Logic Controller) se ha convertido en una herramienta fundamental.
El control PLC consiste en utilizar un dispositivo electrónico programable para controlar y supervisar los diferentes elementos de un sistema automatizado. Estos dispositivos están diseñados específicamente para funcionar en entornos industriales, donde se requiere una alta fiabilidad y resistencia.
Una de las principales ventajas del control PLC es su capacidad para realizar tareas complejas con gran precisión y rapidez. Gracias a su flexibilidad, estos dispositivos pueden adaptarse a diferentes tipos de procesos industriales, desde líneas de producción hasta sistemas de distribución y gestión energética. Además, su programación es altamente personalizable, lo que permite ajustarlos a las necesidades específicas de cada empresa.
Otra ventaja significativa del control PLC es su capacidad para integrarse con otros sistemas y dispositivos. Esto significa que puede interactuar con sensores, actuadores y otros equipos periféricos para recopilar datos en tiempo real y tomar decisiones automáticas basadas en ellos. Esta capacidad mejora significativamente la eficiencia operativa al reducir los tiempos de respuesta y minimizar los errores humanos.
La automatización industrial mediante el control PLC también tiene un impacto positivo en términos económicos. Al optimizar los procesos productivos, se reducen los costos asociados con el desperdicio de materiales, la mano de obra innecesaria y los tiempos de inactividad. Además, al mejorar la calidad de los productos y la precisión en las operaciones, se aumenta la satisfacción del cliente y se fortalece la reputación de la empresa.
Es importante destacar que el control PLC no solo es beneficioso para grandes empresas industriales, sino que también puede ser implementado en pequeñas y medianas empresas. Gracias a su escalabilidad, estos sistemas pueden adaptarse a diferentes tamaños y niveles de complejidad.
En resumen, el control PLC es una tecnología que ha revolucionado la automatización industrial. Su capacidad para realizar tareas complejas con precisión y rapidez, su integración con otros sistemas y dispositivos, así como su impacto económico positivo, lo convierten en una herramienta indispensable para mejorar la eficiencia y productividad en cualquier empresa. Aquellas compañías que deseen mantenerse competitivas en el mercado actual no pueden pasar por alto las ventajas que ofrece esta tecnología. La automatización industrial mediante el control PLC abre un mundo de posibilidades para optimizar los procesos productivos y alcanzar nuevos niveles de eficiencia.
8 Preguntas Frecuentes sobre el Control PLC y la Automatización Industrial
- ¿Qué es un PLC?
- ¿Cómo funciona un PLC?
- ¿Cuáles son las principales características de los PLCs?
- ¿Cuáles son los componentes principales de un sistema de automatización industrial con PLC?
- ¿Qué ventajas ofrece la automatización industrial con PLCs?
- ¿Qué es el lenguaje de programación utilizado para programar PLCs?
- ¿Cómo se realiza la instalación y configuración de un sistema basado en PLCs?
- ¿Cuáles son los pasos para realizar la depuración y pruebas a un sistema basado en PLCs?
¿Qué es un PLC?
Un PLC (Programmable Logic Controller) es un dispositivo electrónico programable utilizado en la automatización industrial para controlar y supervisar diferentes procesos y sistemas. También se le conoce como controlador lógico programable.
El PLC está diseñado para funcionar en entornos industriales, donde se requiere una alta fiabilidad y resistencia. Su principal función es recibir señales de entrada de sensores y otros dispositivos periféricos, procesar la información según el programa preestablecido y enviar señales de salida a actuadores y otros equipos para realizar acciones específicas.
El PLC consta de una unidad central de procesamiento (CPU), que ejecuta el programa almacenado en su memoria, módulos de entrada para recibir señales del entorno, módulos de salida para enviar señales a los dispositivos externos, y una interfaz de comunicación para intercambiar datos con otros sistemas.
La programación del PLC se realiza mediante software especializado, que permite definir las instrucciones lógicas y secuenciales necesarias para controlar el proceso industrial. Los lenguajes más comunes utilizados en la programación son el lenguaje de contactos (ladder diagram), el lenguaje estructurado (structured text) y los diagramas de bloques funcionales (function block diagram).
Una de las principales ventajas del PLC es su flexibilidad y capacidad de adaptación a diferentes aplicaciones industriales. Puede ser utilizado en una amplia variedad de sectores como manufactura, energía, automatización de edificios, procesamiento químico, entre otros.
Además, el PLC ofrece beneficios como la capacidad para realizar tareas complejas con precisión y rapidez, la integración con otros sistemas y dispositivos periféricos, la posibilidad de recopilar y analizar datos en tiempo real, y la facilidad para realizar modificaciones y actualizaciones en el programa.
En resumen, un PLC es un dispositivo electrónico programable utilizado en la automatización industrial para controlar y supervisar procesos y sistemas. Su flexibilidad, capacidad de adaptación y funcionalidades avanzadas lo convierten en una herramienta fundamental para mejorar la eficiencia, productividad y seguridad en el entorno industrial.
¿Cómo funciona un PLC?
Un PLC (Programmable Logic Controller) es un dispositivo electrónico programable que se utiliza para controlar y supervisar diferentes elementos de un sistema automatizado en la industria. A continuación, te explicaré cómo funciona un PLC de manera general:
- Entradas: El PLC recibe señales de entrada provenientes de sensores, interruptores u otros dispositivos. Estas señales pueden ser analógicas o digitales y representan el estado o la condición de los elementos que se desean controlar.
- Procesamiento: Una vez que el PLC recibe las señales de entrada, su procesador interno ejecuta el programa almacenado en su memoria. Este programa está escrito en un lenguaje específico llamado lenguaje de programación ladder, similar a un diagrama de circuitos eléctricos.
- Lógica y control: El programa del PLC contiene instrucciones lógicas que determinan cómo se deben procesar las señales de entrada y qué acciones deben realizarse en función de ellas. Estas instrucciones pueden incluir operaciones matemáticas, comparaciones, temporizadores, contadores, entre otras.
- Salidas: Una vez que el programa ha sido ejecutado y se han tomado las decisiones correspondientes, el PLC envía señales a través de sus salidas hacia actuadores como motores, válvulas o relés. Estas señales activan o desactivan los dispositivos conectados para realizar las acciones físicas necesarias en el sistema automatizado.
- Supervisión y comunicación: Además del control básico, los PLC modernos también pueden supervisar y comunicarse con otros sistemas mediante interfaces como pantallas táctiles o conexiones Ethernet. Esto permite monitorear el estado del sistema en tiempo real, recopilar datos y realizar ajustes en la programación si es necesario.
Es importante destacar que los PLC son dispositivos altamente confiables y robustos, diseñados para funcionar en entornos industriales adversos. También son flexibles y escalables, lo que significa que se pueden adaptar a diferentes aplicaciones y necesidades específicas de cada empresa.
En resumen, un PLC funciona mediante la recepción de señales de entrada, el procesamiento de estas señales mediante un programa lógico interno, la toma de decisiones basadas en dicho programa y el envío de señales de salida hacia los actuadores correspondientes. Esta secuencia permite controlar y supervisar sistemas automatizados en la industria para mejorar la eficiencia y la productividad.
¿Cuáles son las principales características de los PLCs?
Los PLCs (Programmable Logic Controllers) tienen varias características clave que los hacen una opción popular en la automatización industrial. A continuación, se mencionan algunas de las principales características:
- Programabilidad: Los PLCs son dispositivos electrónicos programables que permiten a los usuarios desarrollar y modificar programas para controlar y supervisar los procesos industriales. Esto significa que se pueden adaptar a diferentes aplicaciones y necesidades específicas.
- Flexibilidad: Los PLCs son altamente flexibles y versátiles. Pueden manejar una amplia gama de tareas, desde simples operaciones de encendido/apagado hasta algoritmos complejos de control y lógica matemática. Además, su programación es altamente personalizable, lo que permite ajustarlos a las necesidades específicas de cada sistema o proceso.
- Conectividad: Los PLCs están diseñados para integrarse con otros dispositivos y sistemas en el entorno industrial. Pueden interactuar con sensores, actuadores, pantallas HMI (Human-Machine Interface) y otros equipos periféricos para recopilar datos en tiempo real y tomar decisiones automáticas basadas en ellos.
- Fiabilidad: Los PLCs están diseñados para funcionar en entornos industriales exigentes, donde se requiere una alta fiabilidad y resistencia al polvo, la humedad, las vibraciones y otros factores ambientales adversos. Están construidos con componentes robustos y duraderos para garantizar un rendimiento confiable a largo plazo.
- Escalabilidad: Los PLCs son escalables, lo que significa que se pueden adaptar a diferentes tamaños y niveles de complejidad de los sistemas o procesos industriales. Esto permite que los PLCs se utilicen tanto en pequeñas y medianas empresas como en grandes plantas industriales.
- Diagnóstico y mantenimiento: Los PLCs suelen contar con herramientas de diagnóstico incorporadas que permiten identificar y solucionar problemas de manera eficiente. Además, facilitan el mantenimiento preventivo al proporcionar información sobre el estado de los componentes y la salud del sistema.
- Seguridad: Los PLCs ofrecen funciones de seguridad integradas para garantizar la protección de los trabajadores, los equipos y el entorno. Estas funciones pueden incluir paradas de emergencia, monitoreo de seguridad y protocolos de comunicación seguros.
En resumen, las principales características de los PLCs incluyen su programabilidad, flexibilidad, conectividad, fiabilidad, escalabilidad, capacidades de diagnóstico y mantenimiento, así como funciones integradas de seguridad. Estas características hacen que los PLCs sean una opción confiable y efectiva para la automatización industrial en una amplia gama de aplicaciones.
¿Cuáles son los componentes principales de un sistema de automatización industrial con PLC?
Un sistema de automatización industrial con PLC (Programmable Logic Controller) consta de varios componentes principales que trabajan en conjunto para controlar y supervisar los procesos industriales. Estos componentes incluyen:
- Controlador PLC: Es el cerebro del sistema y se encarga de ejecutar las instrucciones programadas para controlar los diferentes dispositivos y procesos. El controlador PLC puede ser un dispositivo físico o una tarjeta electrónica integrada en un equipo más grande.
- Entradas y salidas (E/S): Son los puntos de conexión entre el controlador PLC y los dispositivos externos, como sensores, actuadores, interruptores, motores, entre otros. Las entradas reciben señales del entorno, como la temperatura o la presión, mientras que las salidas envían señales para activar o desactivar dispositivos.
- Módulos de E/S: Son dispositivos que se conectan al controlador PLC para expandir la capacidad de entradas y salidas del sistema. Estos módulos pueden ser analógicos o digitales, dependiendo de las necesidades del proceso industrial.
- Software de programación: Es una herramienta utilizada para crear el programa lógico que define el comportamiento del sistema automatizado. Permite configurar las entradas y salidas, establecer las condiciones lógicas y definir las acciones a realizar en función de esas condiciones.
- Interfaz hombre-máquina (HMI): Es una pantalla táctil o panel de control que permite a los operarios interactuar con el sistema automatizado. A través del HMI, se pueden visualizar datos en tiempo real, realizar ajustes en los parámetros del proceso e incluso recibir alarmas o notificaciones.
- Redes de comunicación: Son los medios utilizados para transmitir datos entre los diferentes dispositivos del sistema. Pueden ser cables físicos o redes inalámbricas, y permiten la comunicación bidireccional entre el controlador PLC, los módulos de E/S, el HMI y otros componentes del sistema.
- Fuente de alimentación: Es el suministro eléctrico necesario para alimentar todos los componentes del sistema. Debe proporcionar la energía suficiente y estable para garantizar el correcto funcionamiento del controlador PLC y los dispositivos conectados.
Estos son algunos de los componentes principales que conforman un sistema de automatización industrial con PLC. La combinación adecuada de estos componentes depende de las necesidades específicas del proceso industrial a automatizar. Es importante contar con un diseño cuidadoso y una configuración correcta para lograr una automatización eficiente y confiable.
¿Qué ventajas ofrece la automatización industrial con PLCs?
La automatización industrial con PLCs (Programmable Logic Controllers) ofrece una serie de ventajas significativas para las empresas. A continuación, se detallan algunas de las principales ventajas:
- Mayor eficiencia y productividad: Los PLCs permiten optimizar los procesos industriales al realizar tareas complejas de forma rápida y precisa. Esto reduce los tiempos de producción, minimiza los errores humanos y maximiza la eficiencia operativa en general.
- Flexibilidad y personalización: Los PLCs son altamente programables y se pueden adaptar a las necesidades específicas de cada empresa. Esto significa que pueden controlar una amplia gama de sistemas y procesos, desde líneas de producción hasta sistemas de distribución y gestión energética.
- Integración con otros sistemas: Los PLCs tienen la capacidad de interactuar con otros dispositivos y sistemas, como sensores, actuadores, pantallas táctiles, entre otros. Esta integración permite recopilar datos en tiempo real, tomar decisiones automáticas basadas en ellos y mejorar la comunicación entre diferentes componentes del sistema.
- Mayor precisión y calidad: La automatización industrial con PLCs garantiza una mayor precisión en las operaciones al eliminar o reducir los errores humanos. Esto tiene un impacto directo en la calidad final del producto o servicio ofrecido por la empresa.
- Reducción de costos: Al optimizar los procesos productivos, los PLCs ayudan a reducir costos asociados con el desperdicio de materiales, la mano de obra innecesaria y los tiempos de inactividad. Además, al mejorar la calidad del producto, se reduce el riesgo de reprocesamiento o devoluciones por parte del cliente.
- Monitoreo y diagnóstico: Los PLCs permiten monitorear y diagnosticar el rendimiento de los sistemas en tiempo real. Esto facilita la detección temprana de problemas o fallas, lo que permite una intervención rápida y minimiza el tiempo de inactividad no planificado.
- Seguridad mejorada: Los PLCs están diseñados para cumplir con rigurosos estándares de seguridad industrial. Esto garantiza la protección de los trabajadores, los equipos y el entorno laboral en general.
En resumen, la automatización industrial con PLCs ofrece ventajas como mayor eficiencia, flexibilidad, integración con otros sistemas, precisión, calidad mejorada, reducción de costos, monitoreo en tiempo real y seguridad mejorada. Estas ventajas permiten a las empresas optimizar sus procesos productivos y mantenerse competitivas en un mercado cada vez más exigente.
¿Qué es el lenguaje de programación utilizado para programar PLCs?
El lenguaje de programación más comúnmente utilizado para programar PLCs (Programmable Logic Controllers) es el lenguaje de programación en escalera, también conocido como Ladder Logic. Este lenguaje se basa en la representación gráfica de los circuitos eléctricos tradicionales mediante símbolos y contactos, lo que facilita su comprensión y programación para aquellos familiarizados con la electrónica.
Además del lenguaje de programación en escalera, existen otros lenguajes utilizados en la programación de PLCs, como el lenguaje estructurado (Structured Text), que se asemeja a un lenguaje de programación convencional; el lenguaje de bloques funcionales (Function Block Diagram), que permite la reutilización y modularidad del código; y el lenguaje de diagrama de bloques (Sequential Function Chart), que permite una representación visual secuencial del programa.
El uso de un lenguaje específico para programar PLCs tiene varias ventajas. En primer lugar, estos lenguajes están diseñados pensando en las necesidades y requisitos específicos de la automatización industrial, lo que facilita su aplicación en este contexto. Además, estos lenguajes suelen ser intuitivos y fáciles de aprender para los ingenieros y técnicos especializados en automatización.
Cabe mencionar que algunos fabricantes de PLCs también ofrecen sus propios entornos de desarrollo integrados (IDE) con interfaces gráficas intuitivas para facilitar la programación. Estas herramientas suelen incluir editores visuales, simuladores y depuradores que permiten probar y verificar el funcionamiento del programa antes de implementarlo en un sistema real.
En conclusión, el lenguaje de programación más utilizado para programar PLCs es el lenguaje de programación en escalera. Sin embargo, existen otros lenguajes disponibles que permiten una mayor flexibilidad y modularidad en la programación de estos dispositivos. La elección del lenguaje dependerá del fabricante del PLC, las necesidades específicas del proyecto y la experiencia del programador.
¿Cómo se realiza la instalación y configuración de un sistema basado en PLCs?
La instalación y configuración de un sistema basado en PLCs (Programmable Logic Controllers) requiere seguir ciertos pasos para garantizar su correcto funcionamiento. A continuación, te presento una guía básica sobre cómo llevar a cabo este proceso:
- Diseño del sistema: Antes de iniciar la instalación, es importante realizar un diseño detallado del sistema. Esto implica identificar los componentes necesarios, como PLCs, sensores, actuadores y otros dispositivos periféricos. Además, se debe definir la lógica de control y las interconexiones entre los diferentes elementos.
- Montaje físico: Una vez que se ha diseñado el sistema, se procede al montaje físico de los componentes. Esto implica instalar los PLCs en gabinetes adecuados y conectarlos a los dispositivos periféricos mediante cables eléctricos y de comunicación.
- Conexión de alimentación: Es necesario conectar la fuente de alimentación adecuada al sistema para suministrar energía a los PLCs y demás componentes.
- Programación del PLC: La programación del PLC es uno de los pasos más importantes. Se debe utilizar un software específico proporcionado por el fabricante del PLC para crear el programa que controlará el sistema. En este programa se definen las instrucciones lógicas y secuenciales que permitirán el funcionamiento automático del sistema.
- Configuración de E/S: Después de programar el PLC, se deben configurar las entradas y salidas (E/S). Esto implica asignar las señales provenientes de sensores o dispositivos externos como entradas al PLC, así como establecer las salidas que controlarán los actuadores o dispositivos periféricos.
- Pruebas y puesta en marcha: Una vez que la programación y configuración están completas, se deben realizar pruebas para verificar el correcto funcionamiento del sistema. Esto implica simular diferentes situaciones y verificar que las salidas del PLC respondan adecuadamente a las entradas esperadas.
- Monitoreo y ajustes: Después de la puesta en marcha, es importante monitorear el sistema para asegurarse de que cumpla con los objetivos deseados. En caso de ser necesario, se pueden realizar ajustes en la programación o configuración para optimizar su rendimiento.
Es importante mencionar que cada fabricante de PLCs puede tener sus propias particularidades en cuanto a la instalación y configuración. Por lo tanto, es recomendable seguir las instrucciones proporcionadas por el fabricante específico del PLC utilizado.
Además, es fundamental contar con personal capacitado y con experiencia en la instalación y configuración de sistemas basados en PLCs. Si no tienes los conocimientos necesarios, es recomendable buscar asesoría especializada o contratar a profesionales en automatización industrial para garantizar una instalación exitosa.
¿Cuáles son los pasos para realizar la depuración y pruebas a un sistema basado en PLCs?
La depuración y las pruebas son etapas cruciales en el desarrollo de un sistema basado en PLCs (Programmable Logic Controllers). A continuación, te presento los pasos para llevar a cabo este proceso de manera efectiva:
- Revisión del diseño y la programación: Antes de comenzar las pruebas, es importante revisar detenidamente el diseño del sistema y la programación del PLC. Asegúrate de que todos los requisitos y funcionalidades estén correctamente implementados.
- Verificación de conexiones: Antes de encender el sistema, verifica todas las conexiones físicas entre el PLC y los dispositivos periféricos, como sensores, actuadores o interfaces de usuario. Asegúrate de que estén correctamente cableados y conectados.
- Prueba individual de componentes: Realiza pruebas individuales en cada componente del sistema para asegurarte de que funcionen correctamente. Esto incluye probar sensores, actuadores y dispositivos externos para garantizar su correcto funcionamiento.
- Simulación del sistema: Si es posible, utiliza herramientas o software de simulación para probar el comportamiento del sistema antes de implementarlo físicamente. Esto te permitirá identificar posibles errores o fallas sin poner en riesgo los equipos reales.
- Ejecución y monitoreo en tiempo real: Una vez que el sistema está implementado físicamente, ejecuta la programación del PLC y monitorea su comportamiento en tiempo real. Observa cómo interactúa con los diferentes dispositivos periféricos y verifica si cumple con las especificaciones requeridas.
- Depuración de errores: Durante la ejecución del sistema, es posible que surjan errores o fallos inesperados. Utiliza herramientas de depuración proporcionadas por el software del PLC para identificar y solucionar estos problemas. Realiza pruebas específicas para aislar y corregir los errores encontrados.
- Pruebas de rendimiento: Además de verificar el correcto funcionamiento del sistema, es importante realizar pruebas de rendimiento para evaluar su eficiencia y capacidad de respuesta. Estas pruebas pueden incluir la medición de tiempos de ciclo, la velocidad de procesamiento o la capacidad para manejar cargas variables.
- Documentación y registro: Durante todo el proceso de depuración y pruebas, es fundamental llevar un registro detallado de los resultados obtenidos, los errores encontrados y las soluciones implementadas. Esto facilitará futuras referencias y mejoras en el sistema.
Recuerda que cada sistema basado en PLCs puede tener requisitos específicos, por lo que es importante adaptar estos pasos según las necesidades particulares del proyecto. La paciencia, la atención al detalle y la metodología sistemática son clave para garantizar un proceso exitoso de depuración y pruebas en sistemas basados en PLCs.
Leave a Reply